the family that cosplays together stays together at historic ironfest 2019!
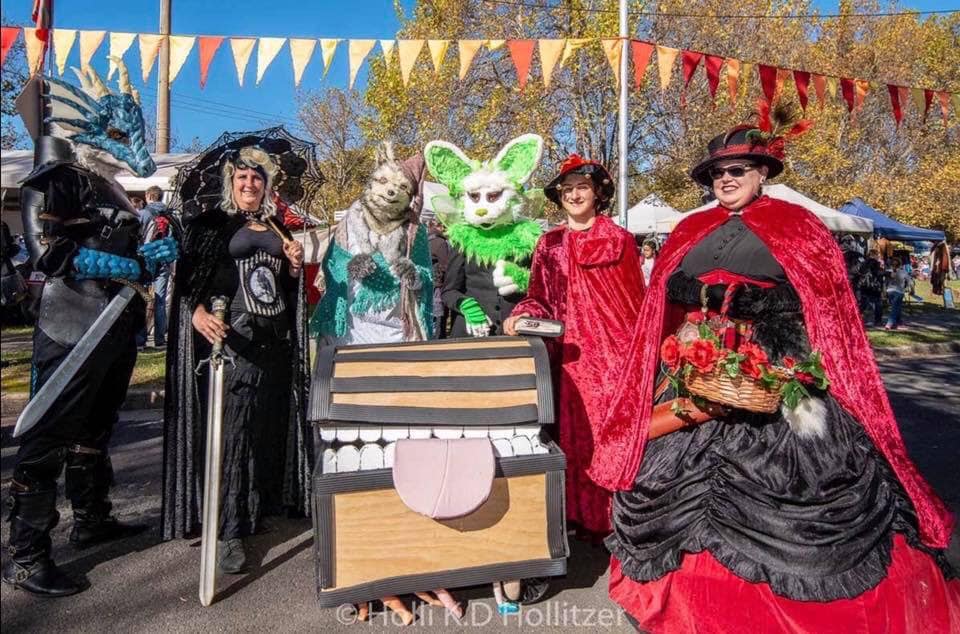
Fantastically cosplayed - all dressed up with a brilliant place to go! The Pierce family - Bea, Adam, Mai and Kai with Draggo (Hugh) the dragon (NSW Furs) and Red Riding Hood (Megan Hodsdon, Sydney Steampunk).
Ironfest began as a glorified art exhibition held in a number of shops in the East End Main Street of Lithgow. The first Ironfest celebrated the birth of steel in Lithgow, steel that was used to build our railways, and involved around 30 artists and performers. It also attracted around 400 people.
The following year it was expanded to include a number of venues outside of Main Street, including the Small Arms Factory Museum, the State Mine Museum, Talisman Gallery, and the Blast Furnace Park; involving around 70 participants and attracting 700 visitors In 2002 Ironfest moved to the State Mine Museum and in this fabulous setting became a real festival involving around 300 people (artists, performers and re-enactors) and attracting in excess of 3,000 visitors.
In 2004 it was forced (because of parking and traffic concerns) to move to its current home at the Lithgow Showground where it has grown exponentially; in 2017 involving over 2,900 participants and attracting close in excess of 17,000 visitors.
Ironfest has had an immeasurable effect on Lithgow’s post-industrial image transforming it from a dirty old coal mining town into a place where quality events take place; many of Ironfest’s participants and acts are now involved in numerous Council run events and locals are proud to promote their town as somewhere worth visiting.
The festival also provides an opportunity for families to have fun together and have fun celebrating Australian History. This year Ironfest is celebrating its 20th year.
As the Ironfest website states:
In a land far, far away, there was a Kingdom hidden deep within a lush valley where a fire breathing dragon turned the very rock to molten steel.
It was here, at the centre of the dragon's lair, that the clans would gather each year at the changing of the season when the leaves streamed red and gold from the trees, and the breeze scattered their richness across the land.
This magical valley was called The Kingdom of Ironfest.
In the twentieth year of the reign of the Kingdom, all creatures great and small, all clans, civilised and wild, are heralded to gather to create the magical story of "Ironfest - Once Upon a Time" in this, the twentieth year of The Kingdom of Ironfest 2019. - Words: Vicki Hartley
Once Upon a Time means stories to many of us and the Pierce family are brilliant at Cosplay; a portmanteau of the words costume play. Cosplay is a performance art in which participants called cosplayers wear costumes and fashion accessories to represent a specific character.
Over the past few weeks Bea has been making 'Catbus' and on the eve of Ironfest 2019 Bea gives a big;
Yay!! Catbus is now a thing - he’s safely stabled and ready to roll tomorrow.
and also;
You know, no artist truly works alone, especially not when making something of this scale. Big thanks to my family - it’s been a group effort! Maia has contributed much of her furry costume making knowledge and made his nose. Kai has helped lug stuff and help me take the skin on and off multiple times (believe me - it’s heavy and like wrestling a dead bear) and of course my partner in crime as always is Adam, who had the engineering challenge of constructing the frame and making it all work!
That's Team Pierce - Family Pierce for you!
Bea Pierce is a multimedia artist and designer, proven design thinker, innovative conceptual ideas creator and stimulator of imaginings, who has been creating and surrounding fortunate others with her inherent aptitude for communicating the glorious for over 20 years.
Through her Jellybeaps alter ego, this artist, photographer and storyteller shares photo essays, stories for children, stories for adults and photographic images you can just fall into - one of our favourites is "Tree Corset" - created during Shona Wilson‘s “Collaborations with Nature” ephemeral land art workshop at Eramboo, Terrey Hills, in 2014.
Readers may recall the 'Doorhenge' interactive art installation Bea created for the Wild Temple of Yam Festival in 2016.
Catbus!
The Catbus (Nekobasu) (referred to in the film as Neko no basu) is a character in the Studio Ghibli film My Neighbor Totoro, directed by Hayao Miyazaki. It is a large creature, depicted as a grinning, twelve legged cat with a hollow body that serves as a bus, complete with windows and seats coated with fur, and a large, bushy tail. The character's popularity has led to its use in a spinoff film, toys for children, an art car, and being featured in the Ghibli Museum, among other products and influences.
A window stretches to become a door when a person would like to board it to travel. With its multiple caterpillar-like legs, it runs, flies, bounces, and hops across forests and lakes to reach its destination, making whole rice fields sway in its wake. Its eyes shine a yellow light brightly like headlamps to guide it. Mice with glowing eyes suspended next to its destination sign on its back and from its rear serve as tail lights. The Catbus is seemingly able to take its passengers to any destination they desire, even if the passenger (or the bus itself) lacks the knowledge how to get there; as is the case when Satsuki needed to find her sister, Mei.
With its large elongated smile and its ability to appear and disappear at will, the Catbus is reminiscent of the Cheshire Cat from Alice in Wonderland. Often used to transport Totoros, in the film it makes an exception to help O-Totoro, the main Totoro, who is also the biggest. O-Totoro calls the Catbus and asks it to help Satsuki find her lost sister Mei. As Satsuki boards it, its destination sign changes to "Mei." After the sisters are reunited, the Catbus volunteers to whisk Mei and Satsuki over the countryside to see their hospitalised mother. After Satsuki and Mei return home, the Catbus finally leaves them, its body fading into the evening shadows.
Why Catbus we asked Bea?
Bea Pierce: Because the theme this year is Once Upon a Time, we’re with NSW Furs (Steam Punk) and we’re all big Studio Ghibli fans. We’re also big Terrey Pratchett and Discworld fans, hence Rincewind and the Luggage.
The Catbus is nearly 7ft x 4ft from head to tail. The frame is constructed from bamboo and electrical conduit. I’m not sure how much it weighs, but believe me it’s heavy! Designed to be a 4-person costume, it operates a little like the Flintstone’s car and also has a wagging tail.
Catbus’s luxurious fur coat is thanks to Emma's Bears. Other materials suppliers include Spotlight, Bunnings, Officeworks and Clark Rubber.
NSW Furs at Ironfest 2019
Rincewind is a fictional character appearing in several of the Discworld novels by Terry Pratchett. He is a failed student at the Unseen University for wizards in Ankh-Morpork, and is often described by scholars as "the magical equivalent to the number zero He spends most of his time running away from bands of people who want to kill him for various reasons. The fact that he's still alive and running is explained in that, although he was born with a wizard's spirit, he has the body of a long-distance sprinter.
Pratchett has said that Rincewind's job is "to meet more interesting people", saying that there is not much he can do with a character who's a coward and doesn't care who knows it.
The NSW Furs allegiance is also probably why husband Adam is dressed as the big bad wolf dressed in grandma's/granda's clothes.... and this little darling furby strolls with him.
Bea: This is Maia’s outfit is all her own original creation - she made it herself. She’s 14. Adam is the Keytar Wolf - usually seen in a dashing steampunk suit and top hat, and sporting a homemade keytar, this year he also dressed as Granny / The Big Bad Wolf!
Keytar!
Steam Punk is a genre of science fiction that has a historical setting and typically features steam-powered machinery rather than advanced technology and also a style of design and fashion that combines historical elements with anachronistic technological features inspired by science fiction. So, very very Ironfest!
For the 2019 Ironfest Cosplayers have a set of rules for their competition:
Cosplay will be alive and well at Ironfest in 2019. We encourage everyone to dress up and join in the fun!
This year’s cosplay competition is going to be the biggest yet.
So what can you expect?
- A competition that welcomes cosplayers of all sizes, levels of skill, backgrounds, genres, etc.
- A competition that welcomes and encourages new cosplayers.
- A competition that allows you to bring in those oversized weapons, blunt metal swords, and realistic guns they always tell you to keep out of other conventions.
THE IRON CROSS
This award is for the best overall Cosplayer of Ironfest. It will be judged from the winners of best overall in each section over the two days.
BLACKSMITH
This competition is intended for the hardcore cosplay elite. All costumes must be at least 50% - 70% home-made by the wearers. Evidence of the costume construction process may be requested. This would include evidence like a build diary, progress pictures and/or patterns.
APPRENTICE
This competition is for those who source AND assemble their costumes. They must be both sourced AND assembled by the wearers. If your cosplay consists of clothing brought from major retailers, fashion houses or clothing stores and assembled for a certain look for your character but requires no significant alterations or modifications to complete the cosplay this is also eligible.
JESTER
This is awarded to the costume and stage presence that gets the best audience response.
JUDGES PICK
This is an encouragement award for the costume which is nearly there but not quite but still deserves recognition.
KIDS COMPETITION (12yrs and under)
We invite all children 12 years and under to take part in our Costume Competition. No need to register for the kid’s competition, just turn up at the Bohemia Marquee ready for the competition at 11.00am each day. Children must be accompanied and supervised by an adult at all times.
JUDGES
Our judging panel this year is made up of three special guest cosplayers! They have the expertise to make decisions based on fairness and industry knowledge.
Judging will be based on:
- Creativity
- Overall design
- Workmanship/finish
- % of costume handmade v’s purchased
- Stage presentation.
We understand there will be lots of great costumes, but not every one can be a winner. Just remember we are here to have fun, to learn from each other and to make connections with people with similar interests.
How cool is that? And yes - the Pierce family make all their own costumes - pretty amazing!
And for further inspiration they have the historic setting of Lithgow itself - I wonder how many original miner-types are there this weekend.... come on now, you didn't think we'd pass up an opportunity to delve into Australia's History did you - especially when Australia is one of the few places you can access the pages from the past to hear from those who were there then?
A little about Lithgow's Iron past:
Lithgow Blast Furnace
The Lithgow Blast Furnace is a heritage-listed former blast furnace and now park and visitor attraction at Inch Street, Lithgow, City of Lithgow, New South Wales, Australia. It was built from 1906 to 1907 by William Sandford Limited. It is also known as Eskbank Ironworks Blast Furnace site; Industrial Archaeological Site. The property is owned by Lithgow City Council. It was added to the New South Wales State Heritage Register on April 2nd, 1999.
History: 1875 to 1900
Lithgow's association with its iron and steel works was another of this city's big manufacturing eras. Its iron and steel works commenced in October 1875 when the first iron smelting took place. Ore had been discovered by Dan Williams on Eskbank land which was then leased by Enoch Hughes, who had previously worked at the Fitzroy Iron Works at Mittagong which produced the iron for the first iron bridge in New South Wales.
RANDOM NOTES.
[BY A WANDERING REPORTER.] IX.
THE last branch of industry, though certainly not the least in importance, should the anticipations of the projectors be at all realised, to which I have to call attention is that of iron smelting. The production of iron in this colony has long excited the attention of gentlemen anxious to develop the resources of the colony, and I am afraid to say how many thousands of pounds have been sunk in the endeavour to establish the Fitzroy Iron Works at Nattai.
Through a variety of circumstances, which I need not here refer to, that endeavour has hitherto proved a failure, though certainly not from any defect in the ore itself. The last trial of the furnace, made by a gentleman specially sent out from England for the purpose of con-ducting the works, proved even more disastrous than any which preceded it, the furnace "bear"-ing up in an incredibly short period. This has been said to be due first to the peculiar character of the ore — a red hematite — of a very rich and valuable description, which turns out "white iron" of the best character; and next from the coal being a pure anthracite, and, as such, altogether unfitted for dealing with ore of this special kind.
THE LITHGOW VALLEY IRON WORKING COMPANY.
The reference of the remarks with which I have commenced this letter to the subject with which I am about to deal will readily be perceived as I go on with my description, not so much of what is being done, as of what it is proposed to do.
The works of this company are situated on the northern side of the railway line, and nearly opposite to Greg's hotel. Owing to the time which has elapsed between my visit to the spot, and the publication of this letter, very much more has been done that I was enabled to report when I was there. However, I shall confine myself to what I then saw, leaving it to some one of your many correspondents to post you up as to the actual advance made to date. The property consists of 100 acres, leased from Mr. Thomas Brown, of Esk Bank. Within some twenty feet of the railway line, a shed 120 feet long and 24 feet wide has been constructed for drying bricks, and men were just then employed for the purpose of making them. Fire bricks for the furnace were to be made in the first instance, and after that ordinary bricks for the construction of offices, residences, &c. Immediately contiguous to the shed a Chilian mill is erected, for grinding the fire-clay prior to its being used in the brick-making. This clay is to be obtained in quantity on the very spot on which the Chilian mill is erected, whilst nature almost seems to have pointed out this spot specially as one on which to erect works of this description. Sandstone of the best quality for building purposes is there; at a depth of only 6 or 8 feet, a seam of excellent coal for coking 14 inches thick has been found, lying on a 6-feet seam of fire clay, and below that again is a bed of common clay suitable for ordinary brickmaking, overlying the main seam of coal, which crops out lower down towards the Farmer's Creek, at a distance of some 50 yards. With regard to the fire-clay, I have before mentioned that the Messrs. Lloyd declared it to be equal to any thing of the kind they had met with in their experience; and I may now say that the manager of this company Mr. Enoch Hughes, who has had many opportunities of judging of the materials required in iron smelting has passed a similar judgment upon it. So convinced indeed was he of its superiority, that he caused a few bricks to be made for the purpose of testing by different persons. One of the these was sent to the Mint, and was returned to Mr. Hughes with the certificate that "it was not to be melted."
These, however, are not all the advantages of the locality, for ironstone is to be found on the ground, of the description known as the "clay band," whilst in the hills adjoining, the red silicious ironstone is to be had in abundance. In fact, the railway cutting, immediately adjoining the bridge by which Bell's line of road is carried across the railway line, has laid bare a belt of ironstone, of the "clay band" character, and about 4 feet thick, though divided by two narrow bolts of micaceous sandstone. The supply of ironstone, however, will not be drawn exclusively from the valley, for in order to avert the difficulties which have stood in the way of the progress of the Fitzroy mines, the clay bands of the valley will be mixed with the "red hematite" of Mount Victoria, the "micaceous" ore of Tarana, and the "magnetic" ore of Mount Lambie, as it is con-ceived that the combination will be much more readily dealt with than would any one of the ores separately. By way of showing the quality of the ore, I will give you a few of the assays made by Mr. Charles H. Cawse, of Bathurst, on the part of the company, before they decided upon taking the matter up. No. 1. schistose, impregnated with bitumen — black band — from Bowenfels, gave 21.75 per cent. of iron; No. 2, red silicious iron ore, from Mount Victoria, gave 13.10 per cent.; No. 3, micaceous iron ore, from Tarana, gave 25.9 per cent.; No. 4, magnetic iron ore, from Mount Lambie, gave 58.6 per cent.; No. 5, clay ironstone (clay band), from Wallerawang, gave 39 per cent.; No. 6, ditto, from Lithgow Valley, gave 49 per cent.; No. 7, ditto, from Mount Victoria, gave 21.3 per cent.
It will thus be seen that ironstone of very high percentage, and in any quantity, is to be had in close proximity to the railway line both up and down, and that the only thing which now remains is to test the applicability of the coal to the purposes of iron smelting. Mr. Hughes is most decidedly of opinion that it will prove all that can be desired; whilst from its so well answering the purpose in the copper smelting furnaces, the inference would certainly be that it would be equally as efficacious for iron smelting. With regard to limestone, the nearest point at which it can he procured is the limestone reserve, situated some six or seven miles from the Wallerawang station, but it is believed that no very large quantity of this will be required, as there is a kind of silicious schist on the ground, which it is said will answer admirably as a flux for the ironstone, when mixed with a pro-portion of limestone.
Having thus dealt with the material, let me now go on with my description of the works. The furnace, the foundation for which was just dug out when I was on the ground, is to be erected in close proximity to the old adit, by means of which, as I mentioned in a former letter, the Esk Bank colliery, was originally worked. It will be 45 feet high, or with the foundation and furnace bed, 55 feet, and being placed by a hill side, will have a convenient run in for feeding at the top. It is planned to be 12 feet across the boshes, and at this size, with the mixed ironstone it is intended to use, it is calculated that it will run to something like 120 tons of iron per week. The engine for working the blast furnace, and the blast furnace itself, will of course be in close proximity to the smelting furnace, and the creek being close handy, a plentiful supply of water, for all necessary purposes will be readily obtainable.
There is of course, in all matters of this kind no test like actual experience, and calculations which are so easily made on paper, are but too often liable to be capsized by some little adventitious circumstance which was thought to be too insignificant in the first instance to be taken into account; but as far as this company is concerned, I honestly believe that the only question to be solved is that of the suitability of the coal. Should this prove what it is expected to be, their calculations, which have been shown to me, and which have been made not by one, but by several gentlemen well up in the iron smelting business, go to prove that even with the present heavy charges for haulage per train, iron could be produced at Bowenfels from the valuable ores in the vicinity, at such a price as would enable it to be sent home to England, and sold there at a lower rate than English iron is now fetching. The company intend in the first instance to produce nothing but common pig iron; but as the works progress, and the character of the various ores are better comprehended, some of the best white iron will no doubt be run from the Mount Victorian hematite. This kind of iron is very much in demand for the shoes of the stampers of quartz-crushing batteries, and for other work where more than usual durability is required, and there exists a very large demand for it not only here but in California. But handsomely as the production of this quality of iron will be sure to pay, the company are acting wisely when they deter-mine to mix the ores, and thus produce, at first, only the ordinary pig for casting purposes.
The gentlemen who have started this company, some eight or ten only in number, I believe, will certainly do a great service to the colony if they succeed in establishing this very valuable industry in the colony; whilst, as far as Lithgow Valley is concerned, they will render it a place of the first importance in New South Wales. With this company a success, there will be sure to be iron smelting furnaces erected in connection with every one of the coal mining companies in the valley, for by that means they will at once be able to convert their coal into the merchantable article of iron, and will thus be altogether independent of any extraneous demand, whilst the valley itself will become a scene of busy life, and add no small amount to our annual wealth.
I had intended to make some remarks upon the coal and ironstone beds in the vicinity of Wallerawang, but this subject has been so recently treated exhaustively by a scientific pen that no observation of mine could be of any value in a field where I, from my particular occupation, can only be a gleaner. RANDOM NOTES. (1875, January 2). The Sydney Morning Herald (NSW : 1842 - 1954), p. 7. Retrieved from http://nla.gov.au/nla.news-article13349127
The foundry was erected nearby after Enoch Hughes convinced James Rutherford, of Cobb & Co. fame, from Bathurst to become involved. The other principal shareholders were the NSW Minister for Public Works, the Hon. John Sutherland and Dan WIlliams, an engineer from Canada who worked on the Lithgow Zig Zag railway project.
The Lithgow Valley Iron Works (later the Eskbank Ironworks) then consisted of a blast furnace, foundry and two bar rolling mills with the necessary fitting and smiths' shops. About 18,000 tonnes (20,000 short tons) of pig iron was made initially from local ores, which was converted into rails and bars. Work was carried on intermittently, until it was decided to pull down the blast furnace and convert the castings into merchant iron.
In May 1880 in the Lithgow Report it stated that the Eskbank Ironworks were working at the rate of four miles of rails per week. The new rails stood the test of 36 tonnes (40 short tons), the required standard being 27 tonnes (30 short tons). The blast furnace was in full swing and 91 tonnes (100 short tons) per week of iron was anticipated.
The original blast furnace at the Eskbank Ironworks closed in 1882, and it is reported that James Rutherford - to avoid the temptation to ever reopen it - in the dead of night, used two dray-loads of blasting powder to blow it up. After the blast furnace closed down, the rolling mills were used to re-roll old iron rails into merchant bars. In 1886, William Sandford, leased the rolling mills at the Eskbank Ironworks to roll rails and then bought the ironworks in 1894.
The Lithgow Blast Furnace was erected by William Sandford in 1906-1907, a short distance from the Eskbank Colliery which he had purchased outright in 1892. The construction of this later furnace over one kilometre (one mile) away from the Colliery was widely criticised, but its proximity to the railway and its size, providing scope for expansion, made it an understandable choice. It was constructed for the sole purpose of smelting iron from ore. It is a popular misconception that the site was also an ironworks. Indeed the Eskbank Colliery furnace, which had been operating since 1875, is often confused with Sandford's later furnace.
After a layoff the mills at the Eskbank Ironworks were restarted on 30 July 1894. The old system had been discarded and the mills had now commenced on a partially co-operative principle, which it was expected would cheapen production and give better results generally. During the cessation of work the plant was added to and improved, in this way the sheet mill now starts equipped to produce nearly double its former product. An order for 91 tonnes (100 short tons) of spike iron, to be supplied at the rate of 9.1 tonnes (10 short tons) weekly, had been obtained from the Railway Commissioners. The company soon found themselves with an overdraft of about A₤60,000 and had decided on closing the works when Sandford took them on lease in 1885. He added mill after mill, with powerful shears, furnaces, boilers and rollers, so that now the mills were fully equipped for the work they had to do. Output for all classes of finished iron and steel for the three years ending 31 December 1901 averaged over 6,400 tonnes (7,000 short tons) per annum. It did not cover more than a small percentage of what was imported into Sydney.
The blast furnace, pictured c. 1900-27, by William Broadhurst; (Source:SLNSW).
The works and sidings occupied a space of about 5 hectares (12 acres), situated between the Main Western Railway Line and Farmer's Creek, being connected with the main line at Eskbank Station, with sidings all round the works. Sand for the works was obtained from Farmer's Creek, close by, and loam for the foundry from a paddock adjoining the works. Within the ironworks' fence is a colliery adit, where the coal was drawn out by an engine, and the same skips drawn around the works, so that coal was only handled once, into the skips; and the same skips were tipped into the furnace bins in the ironworks. Coal was thus used fresh from the colliery, and bore comparison in heating qualities with most of the English coals. On the siding to the works was situated the steam sawmills, where timber of any ordinary size could be cut and delivered to the works.
To heat the iron for the mill, four large furnaces were used, each capable of heating from 4.5–5.4 tonnes (5–6 short tons) of iron per shift. Attached were large horizontal boilers for raising steam by the waste-head from the furnaces. There was a great deal of equipment on site including immense Cornish boilers, weighing 20 tonnes (22 short tons) for raising steam by the waste heat from the furnaces. There was a 1.4-tonne (1.5-short-ton) steam hammer, massive shears for cutting up rails into lengths, a large gantry, 91 centimetres (36 in) horizontal condensing 130-kilowatt (175 hp) engine and giant fly-wheels with 9 metres (30 ft) diameters, weighing 36 tonnes (40 short tons).
The No. 2 Sheet Mill had a 32-tonne (35-short-ton) flywheel. In the fitting shops were lathes, screwing, drilling and punching machines, nut and bolt machines, and a complete spike-making machine, where spikes for the Railway Construction Department had been made the previous three years. The foundry department had two large travelling cranes, a large and small cupola and an air furnace. There was also a large Siemens melting furnace, for dealing with scrap, scrap and pig iron. It was complete with a steam travelling crane capable of lifting 6.4-tonne (7-short-ton) cast iron moulds and large wrought iron ladles. Cement used in the works was mostly made at the Cullen Bullen Company's lime and cement works, about 16 kilometres (10 mi) from Lithgow There was another mill principally for rolling sheets for galvanising and corrugating sheets up to 4 metres (12 ft) long and 27 gauge.
Since 1901
On 24 April 1901 Sandford organised a gala dinner to announce that he and his son Esk had successfully tapped the first viable quantities of steel produced in Australia at the Eskbank Ironworks. He had been working Eskbank since the 1880s, and although tapping steel was a triumph, he was nearly exhausted by it. Mr. Sandford felt iron and steel were basic commodities and needed to be boosted, and tried every which way to protect and support his venture. While Lithgow's coal miners were free traders, iron workers and their bosses were protectionists, so, to advance his cause, Sandford ran as a protectionist against Joseph Cook in the 1901 federal parliamentary election. He then tried to convince the NSW government to take over the works.
LITHGOW STEEL FURNACES
LITHGOW. Tuesday.— Slemen's open-heath steel furnace (the only one in Australia, and which has been comparatively recently constructed at a cost of many thousands of pounds) has been shut down, owing to a cable offering steel bars delivered at the works at about 25s per ton under the price at which local steel can be produced. It appears that, owing to the great demand for steel in other parts of the world during the past three years, the price has been ruling high; so that the Eskbank works had a chance. The demand having fallen off abroad, the price of the commodity is now so low that the works are unable to compete. The steel is made partly from Imported pig Iron, and until there is a duty on the imported finished steel bars, the furnace will not be started again. The directors of William Sandford Limited, decided on Thursday that, in view of the uncertainty of the tariff, it was not expedient to so any further with the new work or erecting machinery on the ground, until the tariff was definitely fixed; consequently the men engaged on the new work have been suspended. The governing director, Mr. William Sandford, says that he would never have started the new work, which means an outlay of £50,000, had he not been fully satisfied of having a tariff sufficient to cover the extra cost of manufacturing here. If there is no tariff on the above lines, all the new work will be stopped. LITHGOW STEEL FURNACES (1901, October 30). Evening News (Sydney, NSW : 1869 - 1931), p. 6. Retrieved from http://nla.gov.au/nla.news-article112575254
Finally, when a tender for steel and iron supply became available he bribed three parliamentarians, including WIlliam Holman, to win the contract. Part of that deal included the construction of a blast furnace, to enable production of pig iron for steel. Sandford complied.
The Blast Furnace was "blown in" on 13 May 1907. It was Sandford's proudest moment and won him the title of the father of the Australian steel industry, although others ascribe that title to Enoch Hughes.
Mr. Hughes was a son of Moses Elizabeth Hughes. His father commenced Burwood Pottery after a failed venture at Balmain. Although Enoch seemed to have caused his family some grief and subjected them to court appearances and bankruptcy when he dabbled in their business as well as being litigious against the Lithgow works on being removed, his pure zeal and appetite for work even in the face of adversity must be admired:
AN ARGONAUT OF AUSTRALIAN IRON.
THE LATE MR. ENOCH HUGHES.
With the furnace of the Eskbank Ironworks in full blast, and the establishment of the iron industry in Australia practically a settled thing, fresh interest is created in the history of treating ore in this country and the multitudinous difficulties which had to be surmounted before Mr. Sandford succeeded in bringing his enterprise to such a successful issue.
Foremost in that small devoted band of enthusiasts who persisted in believing in the capabilities of Australia as an iron producer was the late Mr. Enoch Hughes, who died in Melbourne in 1893, when manager of the Australian Gas Retort and Firebrick Manufacturing Company of that city. From the age of 14 Mr. Hughes was associated with the iron industry.
Born in Dudley, Worcestershire, England, he entered the local ironworks on leaving school, and for 14 years occupied positions of increasing importance in the iron producing districts of Great Britain. When he left England for Australia he was engaged at the Spring Vale works, where 1000 tons a week was turned out. A few days after landing in Melbourne in 1858, Mr. Hughes found that in the State of Victoria was an immense quantity of scrap iron, which for lack of opportunities to turn it to profitable use was obtainable at a figure ridiculously low as compared with the prices ruling in Europe. This was Mr. Hughes's opportunity. He lost no time in importing the necessary plant and establishing the first mill in Victoria for the manufacture of bar iron. The works situated in Dudley-street, West Melbourne, were carried on under his management for some years, and at the present day are still in operation.
When he disposed of his interest in these works three years later Mr. Hughes was approached on behalf of a Melbourne syndicate to visit and report upon the Fitzroy Iron-works at Mittagong. His observations gave such promise that a lease of the works was taken, and he guaranteed to produce pig-iron at the rate of 100 tons a week before the expiration of 12 months. This undertaking he carried out successfully, producing the first pig-iron in New South Wales on November 8, 1863. Mr. Hughes remained at the Fitzroy Ironworks until the expense of working and the restricted local demand for iron led to them being closed down, when he super-intended the erection of the machinery of the Pyrmont Ironworks, and for a time managed this concern. After spending a year in the firebrick manufacture, Mr. Hughes visited Lithgow Valley, and there established the works, of which he remained manager from 1875 until 1882. In the last year of his management 7476 tons of pig-iron were produced.
During the following year Mr. Hughes returned to the Fitzroy works at Mittagong, and converted large quantities of the pig-iron made 16 years previously into bar iron, and at a later date he joined Mr. Sandford in securing a lease of the same property for five years to carry out a contract to re-roll 30,000 tons of rails for the New South Wales Government. At the conclusion of this contract Mr. Hughes assumed control of the Onehunga works in New Zealand. From 1887 until 1891 he acted as manager of these works, relinquishing the position only to take up the position with the Melbourne firebrick manufacturing concern, which he held at the time of his death.
Mr. Hughes was a gentleman known and respected throughout every branch of the iron trade in Australia and New Zealand, and his name will go down in the industrial history of the Commonwealth as one of those whose indefatigable perseverance in the face of tremendous difficulties did much to pave the way for the success inherited by a later generation. AN ARGONAUT OF AUSTRALIAN IRON. (1907, May 16). The Sydney Morning Herald (NSW : 1842 - 1954), p. 8. Retrieved from http://nla.gov.au/nla.news-article14857226
Mr. Sandford's relations with workers were relatively harmonious and beneficent and the Eskbank estate was, to him, a satisfyingly noisy and smoky place. Behind the scenes, Sandford was financially and mentally strained. He could not raise capital but was unwilling to cede his management to external investors such as John Lysagth Ltd., and although Charles Hoskins and his brother George looked at the plant, they pulled out when they saw the state of the books.
The furnace was officially opened by the premier of New South Wales on May 13th, 1907.
HOW THE WORKS WERE STARTED
TWO GRATEFUL COLONIALS MR. RUTHERFORD'S LOSSES
In view of yesterday's ceremony, it is interesting to recall that Mr. James Rutherford, the Squire of Hereford, was one of the founders of the Eskbank Ironworks, and that but for the financial support which he accorded it in the earlier years of its career it is not improbable that the iron industry would be absent from the coaly town of the Blue Mountains to-day.
Chatting with a NATIONAL ADVOCATE reporter, a few days ago, Mr. Rutherford narrated some interesting historical facts concerning the works.
ORIGIN OF THE WORKS.
"In 1874" he said, "I made the acquaintance of the late Mr. Dan Williams, who was at that time carrying out the contract of doubling the railway track through Lithgow Valley, and we decided, as the result of several discussions, that, as the colony had been good to both of us, we would give vent to our feelings of gratitude, and do something for the colony by establishing an ironworks at Eskbank. We — - ' our preparedness to risk £ the project. Having met Enoch Hughes, who professed to be an iron expert, we secured, through him, a lease of 100 acres on terms of 50 years. The trio was joined by the late Hon. John Sutherland, the late Mr. Robert Kelly, of Newtown, the late Mr. J. O. Phillips of Bathurst, and the late Mr. Thomas Denny, late of London. A start was made with so many £500 shares and calls were made as required.
ACQUIREMENT OF COALFIELDS
"Fairly good progress was made for several years, when I foresaw that in order to ensure continued success we would have to acquire coalfields of our own. With our own capital, I then purchased for £45,000, 800 and odd acres of coal land on either side of the railway for a distance of two or three miles, and supplied the Company with coal at 5s. per ton, instead of 6s. 6d. per ton, as we had previously been pay-in g With the blast furnace in operation, this reduction in the price of coal meant a considerable saving in the production of iron.
A HUGE OVERDRAFT
"As time wore on other business precluded me from paying much attention to the works, but everything appeared to be going on all right, until one morning I received a letter from Mr. T. A. Dibbs, General Manager of the Commercial Bank of Sydney, which read something like this: "My dear Mr. Rutherford, I find that the Eskbank Iron Company's account is now overdrawn by £75,000, and with-out some tangible security I shall be obliged to advise my Board not to allow it to be increased." This startling intimation came as a surprise to me, as the last balance-sheet seen by me disclosed an overdraft of only £25,000 to £30,000, and on that occasion I had complained that I would stop the Company's coal ac-count unless the money was forth-coming. I received promissory notes for the large amount owing, and in due time it was paid. On receipt of Mr. Dibbs' letter, I immediately perceived that the payment of this huge sum (£75,000) as well as the floating liabilities of £25,000 must devolve upon Mr. Dan Williams and myself.
THE COMPANY DECEIVED
I immediately went to Lithgow, and, taking stock as well as I could, I found that the Company had been deceived. Hon. John Sutherland, an old gentleman nearly laid on the shelf, was managing director at the time, at a salary of £750 a year. Mr. Enoch Hughes, who was the original manager of the works, had been too much for the Honorable John, supplying him with false returns of stock and material in hand, so as to make his account balance. His returns showed that the stock was worth something like £84,000, whereas, according to the real valuation, it was worth less than £20,000. Mr. Dan Williams had gone to the old country ill, and Mr. Edwin Weinholt, came down to represent him. The new man was anxious to pay the money up, sustaining a loss in the process, and dispose of the property. The amount of money owing was so much that I could not afford to lose it at that time, and, as a result of the stand taken by me, the property was not sold. We then went to Sydney, where we saw the manager of the Commercial Bank, who was generous enough to say that if we reduced the overdraft by £ 20, 000 he would allow us six months without asking for any more.
MR. RUTHERFORD AS MANAGER
"The whole of the partners, with the exception of Mr. Dan Williams, were then still connected with the works. Immediately afterwards, however, Hon. John. Sutherland, finding how things had gone, resigned the managership, and I was elected managing director pro forma. Mr. Kelly next retired, and soon afterwards I discharged Mr. Hughes.
On September 29, 1882, I became manager of the property, and, at the end of the year had it on a paying basis—that is to say, I was not losing money, but was not paying interest on the large sum that was owing. There was a large foundry engineering shop at the works. I secured a five years' contract from the Government for re-rolling old rails at the rate of 5000 tons a year. Nearly all the water tanks along the railway from Albury to the Northern boundary, were made at the works, and the bylinders for the large bridges at Dubbo were cast there. "While I was recruiting my health in England in 1885, the representatives of Mr. Dan Williams' people and the gentlemen representing my interests called a meeting and decided to sell the property. They advertised it, and handbills were distributed, but as soon as I arrived home I stopped the proposal, and carried the works on myself.
ADVENT OF MR. SANDFORD.
"It was about the latter end of '86 or beginning of '87 that Mr. Sandford made his advent, in quest of some waste plant. He came from Mittagong, but as I had been there many years before, and assured him that there was not sufficient ore there to make iron, Mr. Sandford eventually took a lease of the Eskbank works from me. I leased them to him on royalty. Mr. Sandford went to work there at a nominal salary—what he called 'bread that cheese '—£5 a week. I believed had Mr. Sandford was the man, and everything—plenty of energy and determination—with the exception of money to carry on the works. He met the right sort of man when he met me, because if I did not have the money, I had the credit. He carried on these works under me until 1890. In the meantime, I had paid off all that large sum of money, with the exception of that £20,000 paid by us when I was notified of the big over-draft.
MR SANDFORD PURCHASES THE WORKS.
'Mr. Sandford purchased the works from me in 1890 for £70,000, after I had paid off all the debts, amounting to £100,000 or more. Mr. Sandford was thus able to make an unfettered start. I wish to impress upon the public that I did not dispose of the property to Mr. Sandford because I did not think it would pay. On the other hand, I had every faith in the possibilities of the place, and in support of this I must refer to the fact that I purchased an additional 1200 acres of coal land, which would afford a supply for 150 years. Failing health and a surfeit of other business induced me to effect the sale."
BEFORE THE SALE
Mr. Rutherford reverted to what had taken place before the property was under lease to Mr. Sandford, and before the sale was effected. Continuing he said : "I caused the old blast furnace to be knocked down, as soon as I found it had got so much in debt. It only made 70 tons of iron a week, as com-pared with 500 tons turned out by other furnaces then in existence, and we found that we could import pig iron at about half what it would cost to produce it by this slow process. Later on, when we got the sheet mill—which I had indented four or five years previously—going, the Reid Government gave us a blow by removing the £2 import duty, which had been in operation from time immemorial. The Chamber of Commerce meted out similar treatment to us. The merchants had been selling galvanised iron in Sydney at £21 per ton, but as soon as the sheet mill started they reduced it and reduced it until they brought it down to £16 a ton. This was irrefutable evidence that the free trade merchants did not sell articles at what they could import them for, but at what they could rob the public of. If there were no manufactories in a country, the free trade merchants took advantage of the fact by keeping up the prices. In the case referred to they had been selling iron for £21 and £22 per ton, but as soon as it was being manufactured in the State it fell to £16, and even then the merchants made a good profit. There is no doubt that the protection on iron even now offers so much encouragement to the manufacture of iron that it will not be 20 years before there are furnaces in every State in the Commonwealth. That is what protection does. The greatest protection in the world that merchants have for themselves is free trade. They can do what they like then. "If the Government had not touched that duty of £2 which had been on ever since I knew the country, there would have been four sheet mills working at Lithgow for the last 15 or 20 years.
I forgot to mention that while I was carrying on the works they were idle for about six months owing to a strike.
THE ONLY SURVIVOR
Mr. Rutherford is the only survivor of the founders of the works, the growth of which, from the unpretentious start which he gave them, to their present mammoth proportions, has filled him with delight, although he considers that with protection in their earlier stages they would be of greater magnitude still. Mr. Rutherford expressed the hope that Mr. Sandford would make all the money, and more, than he (Mr. Rutherford) had lost, ten times over. He deserves all he can make.
JAMES RUTHERFORD Esq, J.P. (Only surviving founder of the Eskbank Ironworks.)
HOW THE WORKS WERE STARTED (1907, May 14). National Advocate (Bathurst, NSW : 1889 - 1954), p. 2. Retrieved from http://nla.gov.au/nla.news-article157227070
However William Sandford Limited soon ran into financial trouble and could not fulfil its contract to supply the government with pig-iron, so in 1908 the company was purchased by Hoskins Bros, owners of the premier manufacturer of iron pipes in Australia. They made few initial alterations to the Blast Furnace, although the ironworks underwent substantial changes. The Hoskins also succeeded in having Sandford's government contract transferred to themselves and extended until the end of 1916. Their success prompted them to build 80 coke ovens and a second blast furnace at the eastern end of the site in 1913. The second furnace was a near replica of Sandford's original construction. Fifteen coke ovens were added shortly afterwards to cope with the extra fuel requirements.
Blast Furnaces at Lithgow. Because there are two furnaces shown, this photograph was taken, between 1913 and 1928, during the period the Hoskins owned the plant.
The Hoskins were highly active in the development of the ironworking industry and staunchly opposed the growth of unionism. The Hoskins were clear-sighted about the technological problems of the steel and ironworks, and the labour issues, and had considerable business acumen, but Charles Hoskins was impatient and imperious and provoked industrial unrest as soon as he set foot in Lithgow in 1908. He was also a protectionist, and although his negotiations with government over tariffs were never entirely successful, he did manage to get the Eskbank enterprise onto a solid footing before the surge in production caused by World War I.
The outbreak of WWI saw considerable expansion in operations, although Lithgow's monopoly on iron smelting was about to be seriously challenged by BHP, who opened their Newcastle plant in 1915. However, the opening of a Small Arms factory in Lithgow ensured that the Hoskins' works flourished. A great deal of their profit was ploughed back into the expansion of capacity at the steelworks. In 1923 a fifth blowing engine was added to the original furnace. At 360 tonnes (400 short tons), it was the largest in Australia.
In the mid 1920s, the decision was taken to move operations to Port Kembla, where the natural resource and transport network were more attractive. The Lithgow site was abandoned in 1928, although the last employees were dismissed in 1932.
The Fitzroy Iron Works was the first Iron Smelting works in Australia, built in 1848. From 1848 to around 1910, various owners and lessees attempted to achieve profitable operation but ultimately none succeeded. The Fitzroy Iron Works itself was a commercial failure, but it played a part in laying the foundations of the later success of the Australian iron and steel industry. It was important in the growth of the township of Mittagong, New South Wales, Australia.
Just southwest of the current Mittagong town, the original mine deposit was located just South of the Main Road. The Iron Works were established on the North side old Hume Highway and Mt Alexander. The site of the blast furnace had always been known but the existence of remains of the iron works was not. During excavation work for a new Woolworths store in 2004, the remains of the Iron Works were found. The site was excavated and researched, and the new development was expanded to incorporate the historic artifacts. The displays are viewable in the under-ground car park area.
The Fitzroy Iron Works led to the growth of the town of Mittagong and, in particular, the part of that town once known as ‘New Sheffield’. Building allotments in 'New Sheffield' were sold by the company in 1865, to provide additional funds, due to the difficulty in raising capital. The name of Bessemer Street in this area of the township recalls the iron-making past of Mittagong, as do Ironmines Oval and Ironmines Creek, both of which lie between the sites of the original iron works and the blast furnace. Also located within the area formerly know as 'New Sheffied' is Lake Alexandra, a man-made lake that was originally built to provide water for engines on a tramway operated by the Fitzroy Iron Works. During the time that the iron works land was owned by the Mittagong Land Company, more building allotments were sold,
The lion is the symbol of Mittagong and of its public school Some of Mittagong's sporting teams are known as the Mittagong Lions and use the lion as their symbol. The particular design used most commonly - known as the 'Fitzroy lion' - is very similar to that of the commemorative door-stops cast at the Fitzroy Iron Works in 1864.
Newly built Prince Alfred Bridge at Gundagai in 1867. Etching of the new bridge from a photograph by Mr. A. Smith, jun., of Adelong. Published in The Illustrated Australian News for Home Readers November 26th 1867
The iron cylinders used in the piers of the Prince Alfred Bridge over the Murrumbidgee River at Gundagai are made of cast-iron from the Fitzroy Iron Works. Although no longer a part of the Hume Highway, the bridge - opened in 1867- still stands.
The Prince Alfred Bridge is a wrought iron truss and timber beam road bridge over the Murrumbidgee River and its floodplain at Gundagai, New South Wales.
The bridge was named for the then reigning Queen Victoria's son, Prince Alfred, Duke of Saxe-Coburg and Gotha, who visited Australia and Clontarf in that year (Pittwater visit was 1881), and was built to carry the Great Southern Road (now the Hume Highway) across the Murrumbidgee. As opened in 1867 the bridge had a total length of 1,030 feet (313.9 m), consisting of three wrought iron truss spans each of 103 feet (31.4 m) across the river, two timber southern approach spans each of 30 feet (9.1 m), and twenty-three timber northern approach spans each of 30 feet (9.1 m), rising on a gradient of 1 in 30 from the level of the floodplain.
It was the first iron truss bridge to be built in New South Wales.
There's a lot more research found for Readers in the PDF below but let's get back to the celebration of families and friends having fun at the 20th Ironfest at Lithgow.
Some of this year's Ironfest inspired Catbus fun, as taken by Adam Pierce and friends:
Inside Catbus
Ironfest reinforces what we've been saying all along - History and great books are fun!
Go out and get involved in seeing and being around some - Australia and Pittwater is loaded with it!
Maybe even catch the Catbus to your chosen destination...
Catbus and Rincewind WIN!
Late Breaking News: Sunday April 28th
Bea Pierce : 'Ironfest was fantastic fun. Rincewind and Catbus both won prizes in the cosplay costume competition. It was great to see lots of friends and hang out with fellow cosplay / festival regulars. Way too much awesome stuff was purchased, including dragons, wolvish things, feather headdress, ratbags, yowie hats and a fire ketana!
We’re all very tired and footsore but finally all packed up and on the road home. In the car discussions are all about what we’ll do next year / for our next project(s) - and how to top this year’s effort! '
Congratulations Pierce family - well done!
Rincewind- winner!
Rincewind - hat detail
Rincewind - book detail
Rincewind - luggage - Adam (dad) worked some robotic magic so this followed Rincewind - bringing in the Steam Engines 😎
Some pics of the catbus in action - courtesy Tristan Phipps
![]() |
Lithgow Steel History Research for Ironfest 2019 Celebrations AJG.pdf Size : 1337.315 Kb Type : pdf |
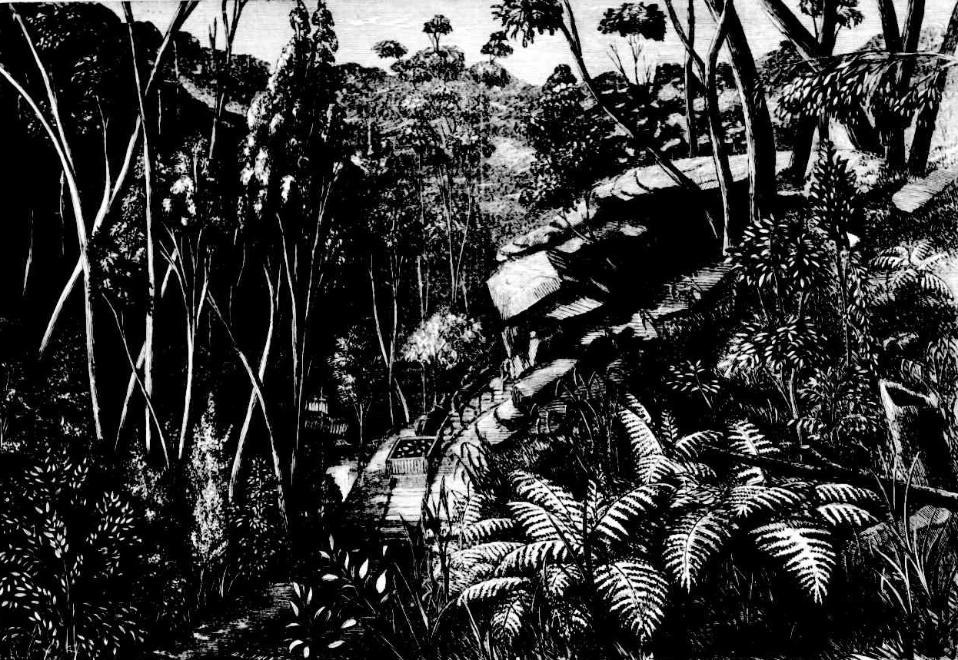
FITZROY IRON MINES — TRAMWAY BETWEEN THE WORKS AND MINE.
Fitzroy Iron Works, Nattai.
[BY OUR SPECIAL REPORTER.]
IT must be nearly a quarter of a century ago since the Fitzroy Iron Mines — 80 miles from Sydney, on the Great Southern Road — were taken up and fortunes were supposed to be looming large before those gentlemen who wore favored with shares in the first venture.
I have before me a mass of information, much of it of a wearisome character, relating to the history of these mines, which are situate in the district I am now visiting. The story is the old, old one. It has often been said that almost every Australian pioneer manufactory or industry has in the first instance resulted in failure, sometimes in great loss, and not in frequetly in positive ruin to many. Unfortunately, the Fitzroy Iron Mines are no exception to the rule. "We have "the e'er true tale" of the man who discovered the mine, the speculators who took up the land and floated it into a company-how wealthy men in Sydney wore induced to go into it how English capitalists followed their examples -how costly machinery was purchased and erected - how still more costly theoretical men, with some knowledge but little experience, were sent up to manage the mine-how almost equally costly men, with much old country experience, followed-how both classes blundered or quarrelled with the directors, or among themselves-how meanwhile the shareholders were repeatedly called upon to pay up and how at last the works came to a stand-still, and many were ruined. Then came another era of still more costly mismanagement, when shafts were sunk almost all over the then largely-extended property of the company in search of coal ; when long drives were made into the mountain side ; when men with the most reckless disregard of the laws of geology sank every where but the right place for coal ; how everything was done on a system utterly at variance with all established rules ; how others tried meanwhile to smelt the ore in a truly original manner, the natural result being that the furnaces got choked and the perverse molted iron would not come out ; and how the most ruinous results followed to the second set of shareholders.
The last, but by no means the least, of the blunders made in attempting to these mines is shown in the accompanying engraving. Here is a picturesque scene certainly of a horse tramway over the mountain. It is almost beyond belief that this tramway, about a mile in length, and constructed at a cost of-I am almost afraid to say how many thousands of pounds, was started from the mine and finished before it was established that there was coal at the other end ! The result was of course another miserable failure. This tramway may be regarded ns the culminating point of a great series of blunders. It has been abandoned of course, for it is now proved that although there is a little coal at the terminus it is not worth anything for smelting purposes.
I do not intend in this article to do more than point out that it is impossible the present proprietory can fail to profit by the lessons these facts teach ; and to state that at length a bright prospect of a long and successful career is before the company under the present management. Notwithstanding that at last success is undoubted, one cannot help sympathising with the pioneers who lost so heavily, and have now no prospect of sharing in the profits. Fitzroy Iron Works, Nattai. (1876, March 18). Australian Town and Country Journal (Sydney, NSW : 1870 - 1907), p. 20. Retrieved from http://nla.gov.au/nla.news-article70589912